It is understood that precision and reliability are the primary reasons why mechanical engineers prefer using electric linear actuators over fluid power actuators in critical powertrain applications. But what about in high temperature environments and combustible situations? Some electric linear actuator manufacturers have developed solutions that you may find interesting.
Pneumatic actuators have been the standard for design engineers in hazardous environments due to the lack of an electrical power source. But they are often prone to air leaks, they tend to be larger in size and the stop point precision is not as exacting as their electronic cousins. When precise reliable linear motion is required, electric linear actuation offers some very compelling benefits. Since maintenance and repairs of pneumatic actuators needs to be included into the equation, electric actuators tend to be more durable over time and therefore more economical over the long term.
Making Hazardous Situations More Tolerable
Several manufacturers of explosion proof valve actuators are using NEMA class VII enclosures for the exterior metal castings for certain actuators. This classification of material improves its ability to withstand high impact explosions and prevent penetration from toxic liquids. Flexible designs allow the digital control module, circuitry and critical wiring to be separated from the gear train and mechanical operations of the actuator and therefore can be positioned a safer distance from high temperatures. The most common concerns for analysis include explosions, fire, and shock hazards. Combustible materials such as acetylene, liquefied petroleum gas, hydrogen, methane, propane, alkali metals, magnesium metal, and metallic hydrides, all fall into the hazardous materials category. Today a 120 V linear actuator can be made impenetrable to these hazardous materials and made more compact than the clunkier pneumatic actuators that do similar tasks.
What is Pneumatic Actuation
These types of actuators operate using compressed gas. The compressed gas then generates force and induces motion of a piston. The air compressor serves as the power source of pneumatic actuators. They tend to be simple and durable, and good for high-speed operations. Use of a pneumatic actuator with modern controls typically requires an analog converter for delivering a control signal setpoint. This is a primary drawback since technology developments in the past 10 years has gone beyond this older methodology.
Conclusion
Both pneumatic and electric rotary actuators work best in hazardous situations where there are large air flow dampers involved. A 120 V linear actuator that has been built to NEMA VII specifications and has a flexible electronics compartment is often a wise choice to tight locations were precision and reliability are of utmost importance. There are several electric actuator manufacturers in the USA that are making high quality industrial actuators that are designed specifically for hazardous environments.
Home >
linear actuator
> Industrial Linear Actuators that work best in Hazardous Situations
Thursday, 26 September 2019
Industrial Linear Actuators that work best in Hazardous Situations
About The Author
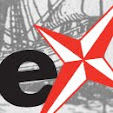
Tom Gilmour
Nulla sagittis convallis arcu. Sed sed nunc. Curabitur consequat. Quisque metus enim, venenatis fermentum, mollis in, porta et, nibh. Duis vulputate elit in elit. Mauris dictum libero id justo.

Labels:
electric actuator,
HBS,
linear actuator
Subscribe to:
Post Comments (Atom)
Popular Posts
-
With the increasing amount of business competition nowadays, emerging as well as seasoned entrepreneurs share the same objective: to gain m...
-
Oftentimes a property owner does not know that their elegant house had been attacked by these little termites till they begin hearing hollow...
-
Weathermen and women have been trying to predict the weather for years using various tools and instruments at their disposal. Mother nature ...
-
Pest infestation can be a persistent problem in commercial facilities and if noticed by clients and patrons, it has the power to destroy a g...
No comments:
Post a Comment