Home >
sheet metal spinning
> The Essentials of Designing and Manufacturing Pressure Vessels
Tuesday, 26 June 2018
The Essentials of Designing and Manufacturing Pressure Vessels
Pressure vessels are designed to contain a volume of fluids or gas in a relatively small space under extreme pressures. They are used in applications ranging from oil extraction to nuclear reactors. No matter how sophisticated the use needs to be, making pressure vessels involves some metal spinning and rolling to get the vessel to have symmetrical cap ends. In fact, the essentials of designing and manufacturing pressure vessels are remarkably similar for any application. Let’s take a look at this video,
Balancing Strength and Practicality
Compressed fluids exert a large amount of strain on their containers. The constant challenge of manufacturing pressure containers is how to balance the strength of the materials with practical constraints such as expansion and weight of fluids under pressure.
Designing strong vessels is addressed in two ways: using strong materials and making the container in a way that the strain is minimized. For the first consideration, steel is the most common solution. It is strong and relatively abundant, making it ideal for manufacturing pressure vessels.
To minimize the strain exerted on the vessel, the solution is conceptually simple when using a round sphere. However, this is often not as simple to engineer. While high-end, specialized pressure vessels can be meticulously manufactured to be perfectly spherical, the majority of applications call for a more tank like solution.
Cylindrical vessels with spherical, “dished,” heads at either end is the most popular way of overcoming this challenge. This design is robust while still being economical to manufacture.
Manufacturing Dished Heads
Making the heads for pressure vessels requires two major steps: creating a mold or metal spinning mandrel and the next step is molding the flat piece of sheet metal around the mold using the process of sheet metal spinning. The first part of this requires the mechanical design to be help the metal spinning manufacturer to create the mold. Most spinning companies start with a block of maple wood for the mold making. The design is programmed into a CNC spinning lathe and machined to the inside dimensions of the metal head.
Following this, the steel can be shaped using a metal spinning machine and an experienced craftsman. The flat sheet metal material is locked into the lathe and the operator get’s the speed up to 750 – 900 rpm’s. At these speeds, the spinning tools are applied at specific angles and force to elongate the sheet metal around the mold’s shape. Once the head ends are shaped, a welder can cut holes for the pressure vessel fluid flow pipes and these are added according to spec and the cap ends can now be added to the pressure vessel body.
When roll forming metal for vessels, the steel material needs to be precut to size prior to entering the roll forming machine. The cap ends that were manufacturers using sheet metal spinning will require good strong welds to prevent any leakage of fluid that will be under pressure. The welding of fixtures and valves to the pressure vessel requires a skilled hand. These weld points will be under the most stress.
About The Author
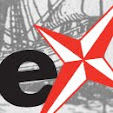
Tom Gilmour
Nulla sagittis convallis arcu. Sed sed nunc. Curabitur consequat. Quisque metus enim, venenatis fermentum, mollis in, porta et, nibh. Duis vulputate elit in elit. Mauris dictum libero id justo.

Labels:
CSC,
roll forming metal,
sheet metal spinning
Subscribe to:
Post Comments (Atom)
Popular Posts
-
With the increasing amount of business competition nowadays, emerging as well as seasoned entrepreneurs share the same objective: to gain m...
-
Oftentimes a property owner does not know that their elegant house had been attacked by these little termites till they begin hearing hollow...
-
Weathermen and women have been trying to predict the weather for years using various tools and instruments at their disposal. Mother nature ...
-
Pest infestation can be a persistent problem in commercial facilities and if noticed by clients and patrons, it has the power to destroy a g...
No comments:
Post a Comment