Mass production of metal parts using progressive die stamping helps manufacturers complete multiple forming operations in a single pass through the press. The stamping dies that are crafted for the bending, piercing and forming of these parts can get very intricate. In order to create the least amount of waste for the strongest result, sheet metal forming companies often have to make several intermediary steps or stages in the metal forming process that minimizes stress on the parts they are making.
Orientation and Rotation
Long run stamping is done on a sheet of metal that is fed through the machine via a roll or coil of metal. There is a need to synchronize the metal pull length with the die stages. Running perpendicular to the metals grain direction is usually the best option, but some amount of rotation may be performed to reduce material waste. Performing a variety of tests and creating multiple samples are useful to determining where the tradeoff in strength and waste lies. No matter how much you save on material costs, you lose out in the long run if your parts durability is minimized.
Keeping It All Together
As parts pass through a progressive die, some scrap between each stage helps carry the entire strip through. This method of "carrying the part," where some scrap is left between each piece, is the most common and produces minimal scrap. Each of the metal stamping companies in Philadelphia we have interviewed for this post manufacturer their dies differently in an effort to get the end result cost effectively.
A different carrying method is to is to use a guide edge to pull the strip through the press and stamp the part die on the other side of the metal strip. This method can create problems in lift since the strip can only be held on one side and a balanced strip progresses more easily than an unbalanced one. This method was far less common with the die stamping companies we interviewed.
Ladder style is the third type of carrying method and it consists of adding material on both sides. This is a balanced version of the second method but can produce much more waste. As with any long run stamping project, a balance must be struck between ease of manufacturing, material strength and material waste.
Exiting the Die
During the design process, it's important not to overlook the act of exiting the die. Some exit strategies involve the part falling naturally off the metal strip, but the balance must be right for this to happen. Any flanges or tabs added can affect the need for any finishing tasks like deburring. It is best to have your tool die makers in house when working with long run stamping dies because the wear and tear on the dies is greater and therefore maintenance is required to extend the life of the dies. Most sheet metal forming companies have a variety of tools and techniques to make the parts a client needs.
Home >
sheet metal forming
> Progressive Metal Stamping Dies Get Complex
Saturday, 17 March 2018
Progressive Metal Stamping Dies Get Complex
About The Author
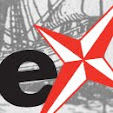
Tom Gilmour
Nulla sagittis convallis arcu. Sed sed nunc. Curabitur consequat. Quisque metus enim, venenatis fermentum, mollis in, porta et, nibh. Duis vulputate elit in elit. Mauris dictum libero id justo.

Labels:
FBF,
metal stamping companies,
sheet metal forming
Subscribe to:
Post Comments (Atom)
Popular Posts
-
With the increasing amount of business competition nowadays, emerging as well as seasoned entrepreneurs share the same objective: to gain m...
-
Oftentimes a property owner does not know that their elegant house had been attacked by these little termites till they begin hearing hollow...
-
Weathermen and women have been trying to predict the weather for years using various tools and instruments at their disposal. Mother nature ...
-
Pest infestation can be a persistent problem in commercial facilities and if noticed by clients and patrons, it has the power to destroy a g...
No comments:
Post a Comment